Introduction
The course of human history has been intricately intertwined with the evolution and utilization of materials, with each advancement shaping cultures and contributing significantly to the growth of civilizations. In recent decades, the exploration of materials at the micro and nano scales has opened up a vast research arena, with nanocomposites emerging as a focal point of scientific inquiry [1,2]. Nanoscience, encompassing the synthesis, characterization, and application of materials at the nanoscale, has become a dynamic field of study [3,4]. The ability to manipulate matter at the molecular level has led to the creation of structures with unique molecular organizations, driving considerable progress in nanomaterial development [5]. The chemical aspects governing nanomaterial formation, such as domain dimensions, molecular mixing at phase boundaries, regularity, and phase consistency, have direct and indirect implications for optical, photocatalytic, antibacterial, physical, and mechanical capabilities [6,7].
Nanoscale materials hold transformative potential, with metal oxide nanoparticles occupying a pivotal role in various applications, including phosphorescence and semiconducting materials, micro-electronic devices, biochemical and optical sensors, as well as energy storage devices like supercapacitors and rechargeable batteries [8–10]. The characteristics of metal oxide nanoparticles are influenced by factors such as particle size, the type of metal used, and reaction parameters, including seeding, nucleation, and annealing temperature [9,11].
Conducting polymers, owing to their unique advantages over conventional materials, have garnered significant attention in recent years. These polymers exhibit wide and variable electrical conductivity, ease of manufacturing, superior mechanical durability, moldability, small weight, affordability, variable molecular weight, permeable nature, high order of conductivity, and ease of material modification [12–14]. Among conducting polymers, polypyrrole (PPy) has gained prominence due to its excellent conductivity, resistance to oxidation, intriguing redox properties, and corrosion protection for various metallic components [18]. PPy serves as a valuable substitute for expensive and energy-intensive semi-metals or replacement metals [15–17]. With pyrrole monomer units that are commercially accessible, readily oxidizable, water-soluble, and possessing favorable chemical characteristics, PPy has found applications in pigment-sensitive solar cells, sensor technologies, memory storage, hybrid capacitors, rechargeable batteries, and more [20,21]. Additionally, PPy is employed in the creation of customized nanoparticle configurations for electrochemical biosensors, storage devices, and metal security [22,23].
The combination of conducting polymers and metal oxide nanoparticles often results in synergistic effects, leading to advanced functional applications across various domains [24–27]. The integration of metal oxide nanoparticles with PPy combines the distinctive properties of both, offering applications in rechargeable batteries, hybrid capacitors, biosensors, chemosensors, optical sensors, adsorption, purification, separation research, antimicrobial and anticorrosive coatings, transducers, and more [28].
In this context, we present a comprehensive study on a nanocomposite material, specifically an electrode material consisting of Gd2O3 embedded in a PPy matrix, resulting in a Gd2O3/PPy composite. The structural and electrochemical characteristics of this composite are thoroughly investigated using X-ray diffraction (XRD), Fourier transform infrared spectroscopy (FTIR), transmission electron microscopy (TEM), cyclic voltammetry, and electrochemical impedance spectroscopy. This research contributes to the expanding knowledge base in nanoscience and underscores the potential applications of Gd2O3/PPy composites in the development of high-performance electrode materials for various energy storage devices.
2. Materials and Methods
2.1 Synthesis
2.1.1 Preparation of polypyrrole
Pyrrole monomer was polymerized using chemically oxidative process where FeCl3 was used as oxidizing agent. Pyrrole (0.2 mol) was agitated in 100 mL distilled water and aq. FeCl3 (0.6 mol) was gradually added to pyrrole solution with continuous stirring (12 h) using a magnetic bar at RT. Resulted black precipitates were vacuum-filtered and were then carefully cleaned with water and ethanol. After that, PPy formed was dried in oven (50 °C) and was transformed into an extremely fine powder [29,30].
2.1.2 Preparation of Gd2O3
Gd2O3 nanoparticles are formed at a lower temperature using a combustion method. Water is utilised as a solvent, while Gd(NO3)3.6H2O and urea are employed as source materials. To create a homogeneous aqueous solution, the estimated quantity of gadolinium nitrate was dissolved into a 100 ml beaker. This solution was then heated at 80 oC. Free water is evaporated during heating, creating a gel–like substance. A measured quantity of urea was then added, along with some distilled water, and a paste was produced before being heated. The purpose of the added urea was to dissolve the metal ions evenly in the reaction solution by forming complexes with them. For around 15 minutes, the paste was heated to 500 oC in a furnace. During the process of heating the material, which produced the product, there was water evaporation, decomposition and gas evolution.
2.1.3 Preparation of PPy-Gd2O3 nanocomposite
To prepare PPy-Gd2O3, in-situ polymerization technique was used including a similar procedure followed for synthesis of polypyrrole. Pyrrole (0.2 mol) was agitated in 100 mL double distilled water and aqueous Gd2O3 (0.5 g) was transferred to the former. The obtained aqueous solution was then ultrasonically sonicated for two hours to allow pyrrole to adsorb on surface of Gd2O3.Then aqueous FeCl3 (0.6 mol) was gradually added to obtained suspension with continuous stirring (12 h) using a magnetic bar at RT. Resulted black precipitates were vacuum-filtered and they were then systematically cleaned with water and ethanol. After that, PPy-Gd2O3 formed was dried in oven (50 °C) and was transformed into an extremely fine powder for various characterizations [30].
2.2 Characterization techniques
The crystalline structure and phase composition of the sample were investigated by recoding the diffraction pattern of samples using Rigaku Ultima-IV diffractometer with Bragg-Brentano geometry using CuKα radiation having wavelength of 1.5416 Ao. X-ray pattern of the materials were recorded from 15o–70o (2 Theta angle) having scanning speed of 2o/minute and 0.02o step interval. The IR spectral profile was recorded using an FTIR spectrometer (PerkinElmer 5700) using KBr as a reference. The morphology and average particle size of the samples was determined by using TECNAI (200 kV) transmission electron microscope (TEM). Elemental analysis and chemical composition of the composite was executed on Ametek (energy dispersive X-ray spectrometer). At a heating rate of 10 oC min-1, prepared samples’ thermograms (30-1000 oC) were recorded using a Hitachi STA 7300 thermogravimetric analyser. Ivium potentiostat was used to understand the redox behaviour of composite material.
3. Results and Discussion
3.1 X-ray diffraction study
Using diffraction analysis, the crystal structure and phase of the prepared samples were determined. The XRD patterns of pure Gd2O3 and a PPy-Gd2O3 nanocomposite are shown in Fig. 1. The synthesis of highly crystalline materials is indicated by the presence of strong diffraction peaks in the XRD profiles. Diffraction pattern of Gd2O3 was found to be closely related to the cubic structure and I213 (199) space group of Gd2O3 with JCPDS 74-1987 [31,32]. Additionally, the lack of foreign peaks in the Gd2O3 diffraction pattern demonstrated the very pure synthesis of the material under consideration. Additionally, a nearly identical diffraction pattern showing no appreciable peak deviations from Gd2O3 was seen for the PPy-Gd2O3 composite material, revealing the homogenous participation of both PPy and Gd2O3 phases in the nanocomposite. The optimal interaction between the various phases in the nanocomposite is demonstrated by a minor change in a few peak positions [33,34].
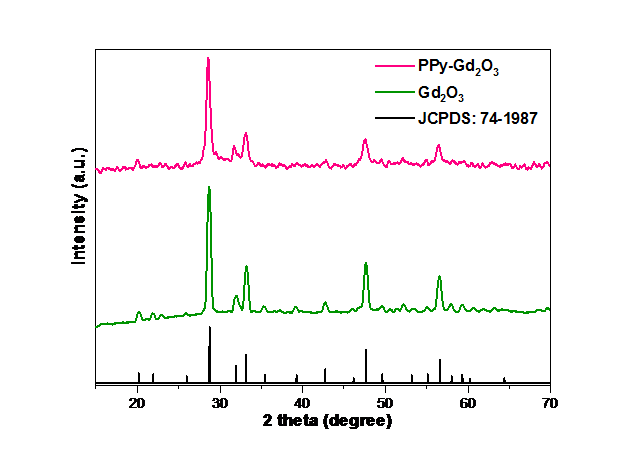
Fig. 1 Diffraction patterns of Gd2O3 and PPy–Gd2O3 matched with JCPDS.
With the help of Scherrer’s formula (Equation 1), the crystal size was calculated from FWHM of the strongest peak. The determined crystal size for Gd2O3 and PPy-Gd2O3 was found to be 40.62 and 37.59 nm respectively.
D = kλ/(β.cosθ) (1)
k = constant,
X-ray wavelength (λ) = 0.15416 nm,
θ = angle of diffraction,
β = full width at half maxima (FWHM),
D = avg. crystallite size.
Table 1 Various diffraction parameters of Gd2O3 and PPy–Gd2O3 samples.
Sample | Area | Width | FWHM (β) | Particle size (nm) |
Gd2O3 | 1096.318 | 0.971 | 1.088 | 40.62 |
PPy–Gd2O3 | 1186.810 | 1.164 | 1.238 | 37.59 |
3.2 FTIR study
FTIR spectrum PPy–Gd2O3 binary composite was recorded to analyse its structural and bonding characteristics. The spectrum was obtained in the 400–4000 cm-1 range as shown in Fig. 2. The spectrum of composite material contains peaks at 815 and 845 cm-1 corresponding to C–H wagging. C=C stretching vibrations are assigned to intense bands at 1514 and 1611 cm-1 for the oxidised states of PPy while C–N and C=N stretching appears at 1391 and 1643 cm-1 in the FTIR spectrum [35,36]. The presence of the quinoid and benzenoid units indicates that PPy is in the conductive emeraldine state. Broad band situated at 3404 cm-1 has been assigned to N–H stretching vibration of PPy [37]. The characteristic peaks corresponding to Gd–O vibrations were observed at 491, 542 and 640 cm-1
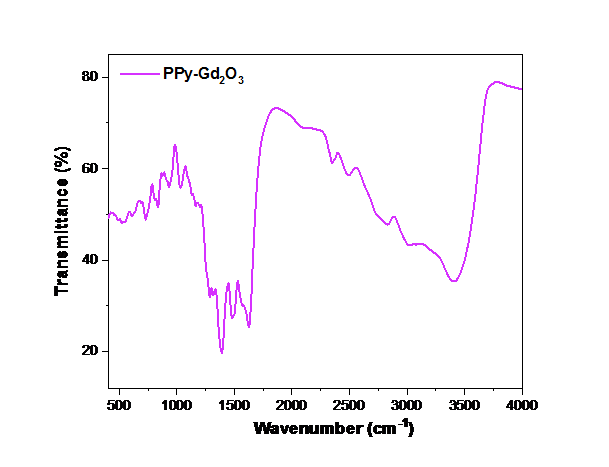
Fig. 2 FTIR spectrum of PPy-Gd2O3 binary composite material..
3.3 TEM investigation
TEM was employed to examine the dimensions and shape of developed composite material. The nearly spherical PPy-Gd2O3 particles are seen in the TEM picture along with some aggregation (Fig. 3). The material exhibits a consistent distribution of particles with a size between 40 and 60 nm. The slightly uneven distribution of mass and heat throughout the synthetic process is what causes the somewhat irregular shape and varied sizes of the particles. This composite material may be useful as supercapacitor electrodes because of the production of nanoparticles.
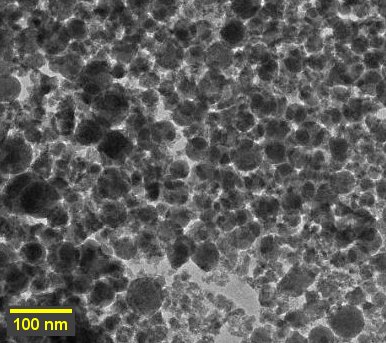
Fig. 3 TEM image of PPy-Gd2O3 binary nanocomposite.
3.4 EDX analysis
EDX analysis was done to verify the preparation of PPy-Gd2O3 nanocomposite. The matching peaks for the elements included in the sample were seen when various parts of the sample were focused, as shown in Fig. 4. Only the peaks in the spectrum that match Gd and O are present. The synthesis of pure PPy-Gd2O3 nanocomposite is confirmed by the lack of peaks that correspond to extraneous components other than the ingredients. Table 2 lists the information related to EDX spectrum of PPy-Gd2O3 in terms of atomic and weight percentages. A homogeneous formation of the material with a suitable elemental dispersion encouraging structural analyses was suggested by the existence of distinctive peaks in the spectrum.
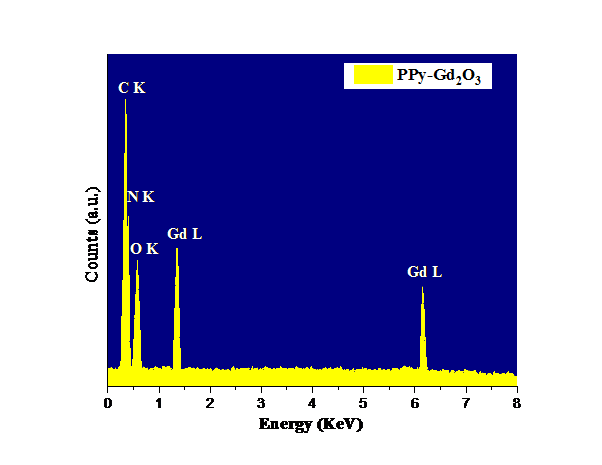
Fig. 4 EDX spectrum of PPy-Gd2O3 nanocomposite.
Table 2 Chemical composition of PPy-Gd2O3 composite in atomic and weight percentage.
Element | Weight % | Atomic % |
C K | 40.98 | 54.87 |
N K | 26.81 | 17.54 |
O K | 18.57 | 15.81 |
Gd L | 13.64 | 11.78 |
3.5 TGA Analysis
To evaluate the thermal stability of the synthesised PPy-Gd2O3, thermo-gravimetric analysis was carried out. The progressive weight loss transition phases, which correspond to moisture loss and the breakdown of organic matter, are revealed in temperatures range 30–600 °C in a N2 environment. At a lower temperature, PPy-Gd2O3 starts to degrade (Fig. 5). For composite, the first weight loss of 3.12 % was noted at 220 °C which involve the elimination of H2O molecules, weight loss of 21.56 % between 220 and 310 °C indicated the elimination of small-molecular-weight oligomers and a decrease in weight of 21.18 % between 310 and 434 °C indicated the decomposition of the nanocomposite matrix. This behaviour could be the result of Gd2O3 particles acting as catalysts, which increase the temperature at which PPy degrades. The interaction between PPy and Gd2O3 is responsible for the PPy-Gd2O3 compound’s excellent thermal stability.

Fig. 5 Thermo-gravimetric curve of PPy-Gd2O3 nanomaterial.
3.5 Current-voltage measurements (I–V)
I–V characteristics of PPy-Gd2O3 binary composite has been depicted in Fig. 6. I–V plot of the considered nanocomposite exhibited outstanding ohmic character at room temperature. The high conductivity of the sample approved it as excellent material for usage in electrode materials for supercapacitor.
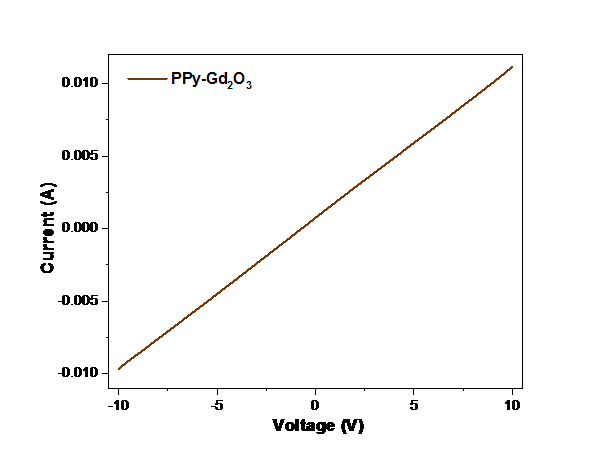
Fig. 6 I–V characteristics plot of PPy-Gd2O3 composite.
3.6 Cyclic voltammetry (CV)
In order to study the electrochemical properties of the PPy-Gd2O3 composite, CV was carried out using a three-electrode cell construction in a 1 molar KOH electrolyte at a voltage (0–0.6 V). Fig. 7 exhibits the cyclic voltammogram of PPy-Gd2O3 nanocomposite having a semi–rectangular loop of higher area indicating its higher value of specific conductance (Csp = 419 Fg−1) calculated as follows:
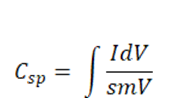
where ∫IdV=area under the CV curve, s=sweep rate (10 mV/s), V=voltage range and m=loaded mass. The inorganic-organic association in nanocomposites, which could potentially improve the redox performance of the constructed electrode, is responsible for a high Csp value.
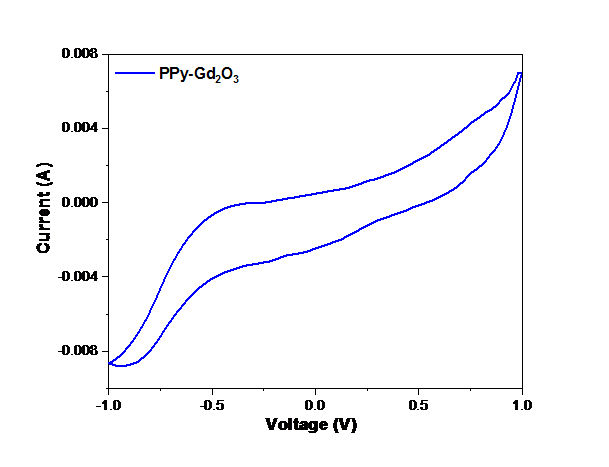
Fig. 7 Cyclic voltammogram of PPy-Gd2O3 binary composite.
3.7 Electrochemical Impedance Spectroscopy (EIS)
The electrochemical behaviour PPy-Gd2O3 binary composite of was further explored using EIS. Nyquist plots (Fig. 8) between Z’ (real part) and Z” (imaginary component) were used to fit the examined data of all three electrode materials in order to get net impedance (z). The linear and quasi-circular region of Nyquist plot are located in low and high-frequency zone respectively. A compact semi-circle with small diameter indicates a high level of ionic conductivity in PPy-Gd2O3 binary composite [38]. I–V findings further supported the greater electrical conductivity. These findings indicate that the charge transfer rate is more important at the interface between the electrode and electrolyte surfaces, which therefore accounts for its high charge storage capability [39,40].
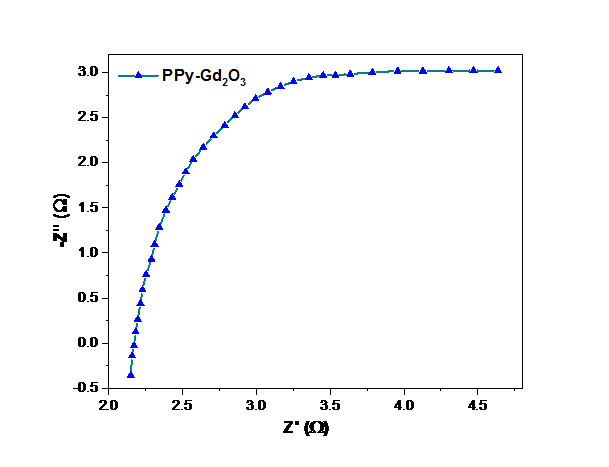
Fig. 8 Nyquist plot of PPy-Gd2O3 binary composite.
Conclusion
PPy–Gd2O3 binary composite was synthesized by the in-situ chemical oxidative method. The prepared material was characterized using XRD, FTIR, TEM, EDX, TGA, cyclic voltammetry and EIS techniques to understand the composition, structural and electrochemical properties. Diffraction data confirmed the synthesis of uncovered and PPy–covered Gd2O3 having cubic structure and I213 (199) space group. FTIR analysis supported XRD results exhibiting vibration bands corresponding to both PPy as well as Gd2O3. TEM images revealed the formation of nanocomposite with some agglomeration. TG analysis exhibited the excellent thermal stability of the sample confirming the possible interaction between PPy and Gd2O3 in the composite. I–V and cyclic voltammetry revealed the high ionic and electrical conductivity alongwith high charge storage capability which were further supported by Nyquist plot of PPy-Gd2O3 nanocomposite. The findings suggest that the PPy–Gd2O3 nanocomposite possesses high charge storage capacity and excellent ionic and electrical conductivity. This makes it a promising candidate for applications as an electrode material in supercapacitors, highlighting its potential in energy storage devices.
Acknowledgement
We extend our sincere gratitude to our Dean for their invaluable assistance and support in conducting the characterization procedures for this research.”
Conflicts of Interest
The authors declare that there is no conflict of interest among them related to the publication of this paper.
References
1. S. Ishaq, M. Moussa, F. Kanwal, M. Ehsan, M. Saleem, T. N. Van, and D. Losic, Sci. Rep. 9, 1 (2019).
2. V. M and G. Velraj, Inorg. Nano-Metal Chem. 0, 1 (2021).
3. C. Ray and T. Pal, J. Mater. Chem. A 5, 9465 (2017).
4. V. Van Tran, T. T. V. Nu, H. R. Jung, and M. Chang, Polymers (Basel). 13, (2021).
5. P. S. Gaikar, K. S. Kadu, K. K. Tehare, G. C. Wadhawa, S. H. Mahmood, and T. L. Lambat, Nanoscale Adv. 4, 5245 (2022).
6. A. Varghese, K. R. S. Devi, S. Mathew, B. Saravanakumar, and D. Pinheiro, Mater. Today Proc. (2023).
7. A. Yadav, H. Kumar, R. Sharma, R. Kumari, G. Kumar, A. Tundwal, A. Dhayal, A. Yadav, and D. Singh, Inorg. Chem. Commun. 158, 111701 (2023).
8. Z. A. Hu, Y. L. Xie, Y. X. Wang, L. P. Mo, Y. Y. Yang, and Z. Y. Zhang, Mater. Chem. Phys. 114, 990 (2009).
9. P. Singh and S. K. Shukla, Surfaces and Interfaces 18, 100410 (2020).
10. G. Sarojini, S. Venkateshbabu, and M. Rajasimman, Chemosphere 278, 130400 (2021).
11. N. Sirotkin and A. Khlyustova, J. Compos. Sci. 7, (2023).
12. P. Sengodu and A. D. Deshmukh, RSC Adv. 5, 42109 (2015).
13. N. Y. Abu-Thabit, J. Chem. Educ. 93, 1606 (2016).
14. A. Thadathil, H. Pradeep, D. Joshy, Y. A. Ismail, and P. Periyat, Mater. Adv. 3, 2990 (2022).
15. K. Namsheer and C. S. Rout, RSC Adv. 11, 5659 (2021).
16. M. El Rhazi, S. Majid, M. Elbasri, F. E. Salih, L. Oularbi, and K. Lafdi, Int. Nano Lett. 8, 79 (2018).
17. A. M. El-naggar, A. Alsaggaf, Z. K. Heiba, A. M. Kamal, A. M. Aldhafiri, A. Fatehmulla, and M. B. Mohamed, Opt. Mater. (Amst). 139, 113771 (2023).
18. K. Jlassi, M. H. Sliem, F. M. Benslimane, N. O. Eltai, and A. M. Abdullah, Prog. Org. Coatings 149, 105918 (2020).
19. N. Jadhav, S. Kasisomayajula, and V. J. Gelling, Front. Mater. 7, 1 (2020).
20. M. Beygisangchin, S. A. Rashid, S. Shafie, A. R. Sadrolhosseini, and H. N. Lim, Polymers (Basel). 13, (2021).
21. G. Shimoga, R. R. Palem, D. S. Choi, E. J. Shin, P. S. Ganesh, G. D. Saratale, R. G. Saratale, S. H. Lee, and S. Y. Kim, Metals (Basel). 11, 1 (2021).
22. J. Zhu, S. Wei, L. Zhang, Y. Mao, J. Ryu, P. Mavinakuli, A. B. Karki, D. P. Young, and Z. Guo, J. Phys. Chem. C 114, 16335 (2010).
23. R. K. Sharma, A. C. Rastogi, and S. B. Desu, Electrochim. Acta 53, 7690 (2008).
24. F. A. G. da Silva Júnior, S. A. Vieira, S. de Avila Botton, M. M. da Costa, and H. P. de Oliveira, Polimeros 30, 1 (2020).
25. P. Liu, J. Yan, Z. Guang, Y. Huang, X. Li, and W. Huang, J. Power Sources 424, 108 (2019).
26. Q. M. Al-Bataineh, A. B. Migdadi, A. Telfah, A. A. Ahmad, A. M. Alsaad, and C. J. Tavares, Mater. Chem. Phys. 290, 2 (2022).
27. Z. Li, J. Li, Y. He, K. Zhou, H. Ji, W. Shi, Y. Sun, T. Wu, and D. Ge, IOP Conf. Ser. Mater. Sci. Eng. 611, (2019).
28. A. Yadav, H. Kumar, R. Kumari, and R. Sharma, Mater. Sci. Eng. B 286, 116085 (2022).
29. A. Batool, F. Kanwal, M. Imran, T. Jamil, and S. A. Siddiqi, Synth. Met. 161, 2753 (2012).
30. M. U. Shariq, A. Husain, M. Khan, and A. Ahmad, Polym. Polym. Compos. 29, S989 (2021).
31. A.K. Jha, K. Prasad, and A.R. Kulkarni, Int. J. Green Nanotechnol. 2, P31 (2010).
32. P. Gribisch, and A. Fissel, RSC Adv. 11, 17526 (2021).
33. R. Nekooie, T. Shamspur, and A. Mostafavi, J. Photochem. Photobiol. A Chem. 407, 113038 (2021).
34. K. B. Yazhini, X. Wang, Q. Zhou, and B. O. Stevy, RSC Adv. 11, 36379 (2021).
35. V. Q. Trung, D. N. Tung, and D. N. Huyen, J. Exp. Nanosci. 4, 213 (2009).
36. M. Joulazadeh and A. H. Navarchian, Synth. Met. 210, 404 (2015).
37. M. A. Chougule, S. G. Pawar, P. R. Godse, R. N. Mulik, S. Sen, and V. B. Patil, Soft Nanosci. Lett. 01, 6 (2011).
38. H. Deng, J. Huang, Z. Hu, X. Chen, D. Huang, and T. Jin, ACS Omega 6, 9426 (2021).
39. M. Naveed ur Rehman, T. Munawar, M. S. Nadeem, F. Mukhtar, U. A. Akbar, S. Manzoor, A. S. Hakeem, M. N. Ashiq, and F. Iqbal, Solid State Sci. 128, 106883 (2022).
40. M. T. Ansar, A. Ali, G. M. Mustafa, F. Afzal, S. Ishaq, F. Kanwal, S. Naseem, and S. Atiq, J. Alloys Compd. 855, 157341 (2021).